How We Got Here: A Brief History of the Resin Shortage
- Inzuri Health
- Mar 26, 2022
- 4 min read
Updated: Apr 1, 2022
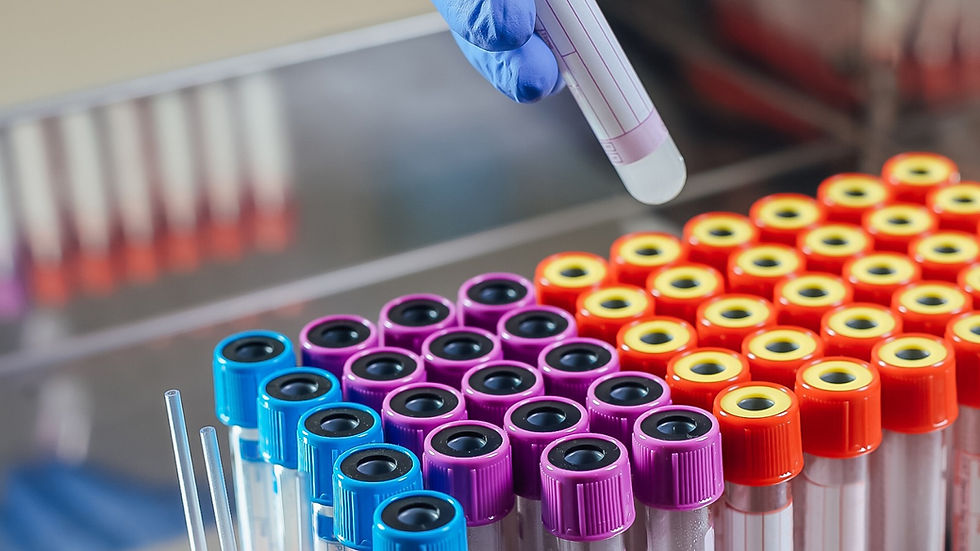
Over the past couple of years, there have been plenty of global events that have greatly affected the resin supply chain. Resin in the medical supply space is crucial in making blood collection tubes, ventilators, masks, hospital bed film linings and frames, medical-grade face shields, and vaccine syringes. Outside of the healthcare industry, resin is used in almost every major industry, notably food and beverage, automotive, and paint.
In the 2nd edition of our How We Got Here series, we will explore factors that have affected the resin supply from the COVID-19 pandemic to the current Russia-Ukraine conflict.
2020: The Pandemic
Resin supply chain shortages both within and outside of the healthcare industry peaked during the pandemic in 2020, when a 50% increase in food and home deliveries, which make heavy use of plastics, reached all time highs. In addition, the demand for 52 billion masks and other medical devices further increased the demand for resin.
Overwhelming fears about future supply combined with a grinding halt of international business caused innumerable issues for supply chains. This was further exacerbated by the mass closure of Chinese factories, which remain the United States’ most crucial supplier of materials and inventory.
Initially, the factory closures seemed manageable given the time of year, as the US typically imports extra materials from China before the Lunar New Year (January/February) in anticipation of planned factory closures. This extra inventory was enough to keep buyers afloat for the first few weeks, but continued factory closures, of course, eventually caught up to them. When Chinese factories were finally given the ‘ok’ to re-open, not only were there a lack of employees to work, but also a shortage of masks/other PPE to ensure safe working conditions. These issues combined with a shortage of necessary raw materials to produce medical products, turned supply chain production delays from a projected 6 weeks to many months.
In late 2020, as resin production began to look like it would eventually catch up with demand, Operation Warp Speed, the US driven initiative to vaccinate the population against COVID-19, added a new strain on resin. Resin is an integral part of vaccine administration as it is used to produce syringes and vials. Approximately 850 million syringes and vials were needed in order to vaccinate the population (not even accounting for booster shots), and the sheer enormity of this mandate was destined to create more supply issues.
American manufacturers importing resin from outside the US were told to expect at least a month delay on shipping times. Some manufacturers reacted to these delays by attempting to cut down on production times by creating pre-filled syringes, using blow-fill-seal technology. Others try to circumvent resin entirely by employing a process called chemical vapor deposition which creates air tight syringes using different plastics and glass. Still these methods did little to mitigate the seismic supply-demand imbalance.
2021: Winter Storms
The healthcare supply chain began to slowly recover or at least adjust to the waves of demand by the end of 2020, only to be hit once again in February 2021. This time, though, an unprecedented winter storm reached Texas and largely the Southeastern part of the US. There were devastating impacts such as loss of life, power, and water. The rippling effects of these impacts led to the shutting down of petrochemical plants and therefore, plastic exports, which account for 78% of supply for the precursor of resin (as resin is made through multiple chemical processes).
Resin is a petroleum byproduct which is an industry heavily concentrated on the Gulf Coast. The storms halted access to materials such as ethylene monomer and silicone, which further impacted the ever-challenged supply chain of medical grade resin. The storm also raised prices between 30-50%, and 75% of polyethylene, 62% of polypropylene, 57% of PVC resin production halted.
2022: Russia-Ukraine Conflict
Resin prices began to level out again in November of 2021, just months before Russia’s invasion of Ukraine caused its own effects on oil prices and shipping costs. As we have already detailed, the resin supply chain is extremely delicate and uniquely susceptible to global events. The Russia-Ukraine conflict has led to a massive national increase in oil and gas prices, and as resin is a fossil fuel derived material, it is therefore also greatly affected by this domino-effect. Resin prices have already gone up at least 6 cents a pound in February, and are forecasted to only rise more.
While we are still in the thick of the Russia-Ukraine conflict, and climbing our way out of the global pandemic (albeit rather slowly), it’s vital that we think of solutions to overcome these issues. Luckily, biotech professionals are already on that, and have come up with some pretty innovative ways to figure this whole thing out. A few have coined some metal-to-plastic conversions using smaller amounts of resin which has allowed for effective products and repeated sterilization. Resin is also highly biocompatible, and they’ve begun testing these new products for joint replacements and bone implants (pretty neat). More broadly, though, companies have focused on discovering alternative materials experimenting with multiple use medical devices, as well as trying to find US suppliers for resin.
How do I protect against resin shortages in healthcare?
It’s essential for supply chain professionals to diversify their supplier base given the uncertainty in global production. Organizations that have formed relationships beyond manufacturers/tier 1 distributors have seen success in sourcing resin-based products. For example, during times of heavy backorders for Cardinal and BD, Inzuri was able to source their products from small and medium-sized distributors who had inventory, but lacked relationships with large hospital systems for distribution. We were also able to leverage our non-med-surg sourcing networks to find non-traditional suppliers who were unique holders of inventory in the US and Canada. This resulted in Inzuri facilitating the delivery of thousands of cases on back-ordered products to hospitals that needed them the most.
In general, broadening relationships with vendors that have a diverse list of procurement categories allows for greater supply chain resiliency when faced with unforeseen scenarios. In a future post, we will discuss some of the top strategies to add the right type of diversity to your list of vendors.
Opmerkingen